Understanding Used Single Screw Extruders:
At the heart of used single screw extruders lies a simple yet highly effective mechanism. These machines consist of a single rotating screw housed within a barrel. The screw rotates within the barrel, pushing the material forward while subjecting it to heat and pressure. As the material moves along the barrel, it undergoes a series of stages, including melting, mixing, and homogenization, before being extruded through a die to form the desired shape.
Components of Used Single Screw Extruders:
Motor: A single screw extruder motor provides power needed to rotate the extruder screw. The motor is often coupled with a gearbox to provide speed and torque control. An optimized motor and gearbox combination results in a well-functioning extruder.
Gearbox: The gearbox for a single screw extruder ensures the operation of the extruder by conveying power from the electric motor to the extruder itself. The end product produced by the single screw extruder relies on a high-quality gearbox, as the gearbox determines the speed and torque of the screw.
Controls: Single screw extruder controls are essential to ensure a high quality plastic product. The controls for the extruder govern functions such as screw speed and barrel temperature. Efficiency and proper functioning for a single screw extruder rely heavily upon the right control system.
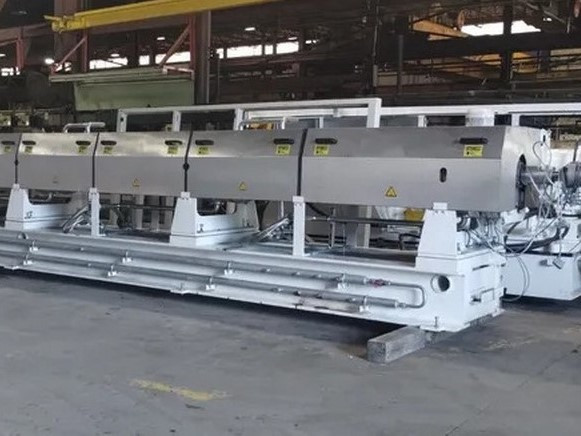
Screw: The screw is the central component responsible for conveying, melting, and mixing the material. It typically consists of several sections, including the feed section, compression section, and metering section, each with specific functions in the extrusion process.
Barrel: The barrel encases the screw and provides the necessary heat and pressure to melt and shape the material. It is often equipped with heating and cooling systems to regulate temperature throughout the extrusion process.
Die: The die determines the final shape and dimensions of the extruded product. It is located at the end of the barrel and features an opening through which the molten material is forced to form the desired profile.
Used single screw extruders are extensively used in the plastic industry for manufacturing products such as pipes, tubes, films, sheets, and profiles. They can process various types of thermoplastics, including polyethylene, polypropylene, PVC, and polystyrene.
Used single screw extruders are utilized in the rubber industry for manufacturing rubber profiles, hoses, seals, and gaskets. They can process different types of rubber compounds, including natural rubber, synthetic rubber, and elastomers. Single screw extruders are employed in the pharmaceutical and chemical sectors for producing pellets, granules, and formulations. They can process a variety of materials, including active pharmaceutical ingredients (APIs), excipients, and specialty chemicals.
Applications:
Used single screw extruders are utilized across various industries due to their versatility and efficiency. In the packaging sector, these extruders are instrumental in the manufacturing of plastic films, sheets, and bags used for packaging applications. In construction, they play a vital role in producing pipes, profiles, and other building materials. The automotive industry benefits from single screw extruders for fabricating components like bumpers, dashboards, and interior trim. Additionally, in the consumer goods sector, they are employed in the manufacturing of household items, toys, and appliances. In agriculture, single screw extruders are crucial for the production of irrigation pipes, greenhouse films, and agricultural nets. Furthermore, they are utilized in the medical field for extruding medical tubing, catheters, and surgical components. Lastly, single screw extruders play a key role in recycling efforts by reprocessing plastic waste into recycled pellets for reuse, contributing to sustainability initiatives across industries.
Advantages:
Used single screw extruders are highly favored in the plastics industry due to a multitude of advantages they offer. Firstly, their versatility is unmatched as they are capable of processing a wide array of thermoplastic materials, additives, and fillers, making them suitable for diverse manufacturing needs. Moreover, these extruders boast remarkable efficiency, characterized by high throughput rates and continuous operation, ultimately leading to cost-effective production processes. Their flexibility is another notable feature, allowing for easy adaptation to various product designs and formulations through simple changes in die and screw configurations. Additionally, precise control over temperature, speed, and pressure ensures consistent product quality and performance, enhancing overall production outcomes. Furthermore, single screw extruders are renowned for their reliability, thanks to their simple design and robust construction, which minimizes downtime and maintenance requirements. Lastly, their scalability is a key advantage, with used extruders available in a range of sizes and configurations to accommodate different production scales and requirements, making them a versatile and indispensable tool in the plastics manufacturing industry.
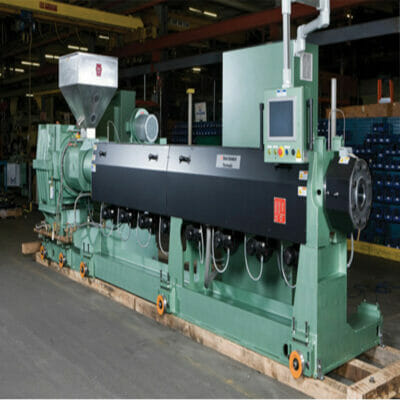
Considerations:
While used single screw extruders offer a multitude of benefits, maximizing their effectiveness requires careful consideration of several factors. Firstly, material compatibility is crucial, necessitating the selection of appropriate extruder configurations and screw designs tailored to the specific properties of the plastic material being processed. Additionally, optimizing process parameters such as temperature, screw speed, and residence time is essential to achieve desired product properties efficiently. Energy consumption is another significant consideration, prompting the implementation of energy-efficient practices and equipment to reduce operating costs and minimize environmental impact. Moreover, regular maintenance and cleaning of extruder components are paramount to prevent wear, contamination, and degradation of product quality over time. Safety remains a top priority, requiring strict adherence to safety protocols and regulations to mitigate the risk of accidents and injuries during operation. Lastly, staying abreast of technological advancements in extrusion technology is imperative, as it enables manufacturers to leverage innovative solutions to enhance productivity, quality, and competitiveness in the dynamic plastics industry landscape.
Used single screw extruders play a critical role in the plastic processing industry, offering versatility, efficiency, and reliability in converting raw materials into a wide range of plastic products. Understanding the functionality, components, applications, advantages, and considerations associated with single screw extruders is essential for manufacturers seeking to optimize their production processes and achieve superior product quality. With continuous innovation and advancements in extrusion technology, single screw extruders remain at the forefront of plastic manufacturing, driving progress and innovation in various industries around the world.